Экскурсия на автомобильный завод BMW в Лейпциге.
Предлагаю вашему вниманию увлекательный рассказ о посещении завода BMW в Лейпциге, одним из пользователей форума 1addicts.com:
Сегодня состоялся наш специальный тур на английском языке, который я давно и с нетерпением ждал! Дело в том, что большинство экскурсий на завод проводятся на немецком языке, с группами свыше сорока человек. Сегодня мне и Kiyo устроили индивидуальную экскурсию. У нас был отличный гид , он показал нам некоторые редкие экспонаты, на которые не все обращают внимание. Мы смогли заглянуть в самые сокровенные места завода BMW.
По сравнению с Лейпцигским заводом, завод BMW в Мюнхене выглядет старым и несовременным. Действительно,интересно то, что баварцы делают большую ставку на Лейпциг и имеют большие планы по расширению производства.
Наш гид объяснил нам, что завод имел четыре основных производственных зала (в BMW называют их "пальцы"). Им нужно было добавить новый зал ... и они добавили еще "большой палец"! (немецкий юмор). Но на самом деле, завод является очень гибким для выпуска новых продуктов.
Далее гид рассказал нам, что в Лейпциге будут производить новые i8 (Vision Concept) и i3 - городские электромобили, сделанные из карбона. Мы увидели некоторые образцы кузовов из углеродного волокна для нового i3/i8 (В 2014 году начнется производство в Лейпциге), а также узнали о планах на будущее расширение завода. Похоже, в BMW не только хотят, производить экономичный автомобиль (i3/i8), но они также планируют сделать завод – лидером в области энергосбережения, переработки и возобновления ресурсов.
Компания BMW планирует установить несколько ветровых электрогенераторов, которые будут обеспечивать нужды завода более чем на 90%. Также начнется строительство четырех новых крупных залов на территории завода. Интересный факт, о котором я не знал – территория завода BMW в Лейпциге в два раза больше исторического центра города.
Мы также видели некоторые образцы углеродных волокон (CF) для крыши новых M3/M6. Наш гид объяснил нам, что каждый килограмм, который сэкономили за счет преимущества в весе CF перед сталью, стоит в семь раз больше, поэтому использовать углеродного волокно приходится только там, где это действительно необходимо. Я, конечно, спросил его, почему в 1М не используется карбоновая крыша ... но он не знал!
Наша экскурсия началась в штамповочном и сварочном цехе. В этом зале стоял жуткий грохот. Было очень здорово видеть (в буквальном смысле) искры, и как панели кузовов, сваренные вместе, обретали очертания автомобиля.
Восемьдесят пять процентов кузовных панелей изготавливаются на заводе. В BMW около 900 + роботов выполняют тяжелую работу - с помощью сварки, соединяют части вместе. В некоторых местах BMW использует эпоксидную смолу, но для большей части применяют старомодную сварку. Я заметил, что для E88 сварка днища поручена людям. Я предполагаю, что когда дело доходит до сложных элементов, люди справляются с этим гораздо лучше, чем роботы!
После того как кузова свариваются, они двигаются по конвейеру через лобби завода и все офисные помещения к окрасочному цеху, а затем на окончательную сборку. Это делается для того, чтобы все сотрудники ощущали свою причастность к общему делу.
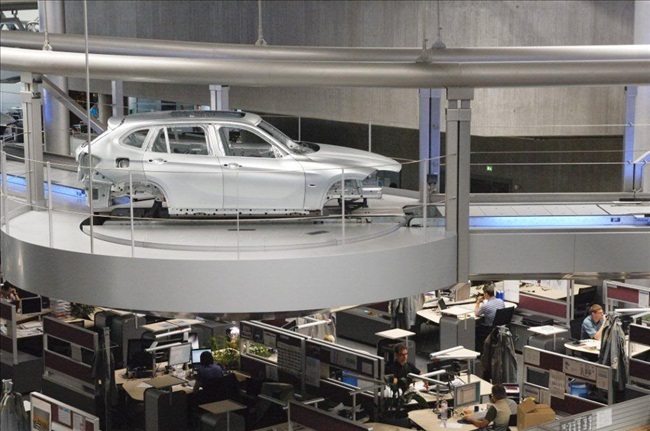
Затем мы посетили окрасочный цех. Обычно в подобных цехах очень грязно и на большинстве автозаводов посторонний человек не сможет попасть в окрасочный цех. Но в BMW конструировали этот завод с расчетом на проведение регулярных экскурсий и у них есть специальный герметичный коридор для туристов, которые могут полюбоваться на только что окрашенные автомобили. Технологии BMW позволяют окрасить один автомобиль в один цвет, а уже на следующий за ним автомобиль изменить цвет!
Здесь стоит отметить, что нам показали четыре этапа окраски: гальванизация, грунтовка, базовый слой, покраска (фактический цвет), нанесение прозрачного покрытия. На стене были представлены образцы "коллора", которые используются на производстве в Лейпциге.
На один из них я обратил внимание - " Mineral White ". Я спросил нашего гида о том, что это за цвет, он ответил, что его используют на 1М! Но я усомнился: «вы имеете в виду Alpine White?». Он сказал, что он почти уверен, что в настоящее время используется Mineral White.
Я также видел " Uni-Schwartz ", который чем-то похож на DSB, но в нем больше черного.
Потом мы посетили пункт контроля качества окраски на конечной стадии. Здесь проверяют качество покраски каждой детали. Тут находилось всего несколько ребят, может быть, десять или около того. Я обратил внимание на две вещи – пол здесь был покрыт деревянным паркетом (что не типично для завода), а каждый работник может потратить столько времени, сколько он или она посчитает нужным, чтобы довести лакокрасочное покрытие автомобиля до идеального состояния.
Работники используют маленькие двухдюймовые диски для мокрой пескоструйной обработки. Затем они тщательно полируют кузовные панели.
После того как сборка закончена ... какой-то процент готовых кузовов отправляется на склад. Это делается для того чтобы иногда при необходимости, изменить штамповочные прессы. И при этом на заводе всегда должен быть некоторый запас готовых кузовов, чтобы конвейер не останавливался. Я думаю, что примерно 900 автомобилей могут храниться внутри завода.
Затем мы прошли через сборочные цеха фабрики в зону "большого пальца", как наш проводник называл это место! Здесь кузова поднимаются на лифте на сборочный конвейер. Первое, на что обращаешь внимание - все двери снимаются и сохраняются для последующего использования. Теперь в машину укладываются жгуты проводов, звукоизоляция, приборная панель и устанавливаются стекла. Впечатляет то, как машину вращают, удерживая её на весу, за счет двух роликов.
Мы поднялись на специальную смотровую площадку, которая расположена над заводскими цехами, вдоль всей "производственной линией" . Отсюда вы можете увидеть, как все рабочие трудятся на сборочном конвейере.
Любопытно, что никто здесь не делает одну и ту же работу целый день. Каждый сотрудник обучен выполнять несколько операций и они меняются каждые 45 минут - чтобы не скучать или не терять концентрацию.
За все время нашей экскурсии мы видели около девяти 1M, собирающихся на заводе сегодня. Большинство из них были окрашены в фирменный цвет Valencia Orange. Но я был удивлен, увидев совсем немного белоснежных автомобилей (Alpine White). Я спросил нашего гида, BMW 1М каких цветов чаще всего заказывают? Он ответил, что большинство машин, которые он видел это Valencia Orange, затем по популярности идет цвет Alpine White, ну а самые редкие м-ки в черном цвете - Black Sapphire Metallic. Я думал, что цвета будут распределяться более равномерно.
По моему, все логично, белый цвет берут чаще, потому что это базовый цвет, за который не нужно доплачивать.
Мы также увидели немало ActiveE – электромобилей на базе купе первой серии E82. Для нас было неожиданностью, насколько сильно отличается передняя часть автомобиля от стандартной версии. Кроме того все ActiveE были окрашены в белый цвет, разумеется без ярких логотипов и полосок, которые мы видели на официальных фотографиях.
Продолжение и еще фотографии можно посмотреть в BMW блоге.
Сегодня состоялся наш специальный тур на английском языке, который я давно и с нетерпением ждал! Дело в том, что большинство экскурсий на завод проводятся на немецком языке, с группами свыше сорока человек. Сегодня мне и Kiyo устроили индивидуальную экскурсию. У нас был отличный гид , он показал нам некоторые редкие экспонаты, на которые не все обращают внимание. Мы смогли заглянуть в самые сокровенные места завода BMW.
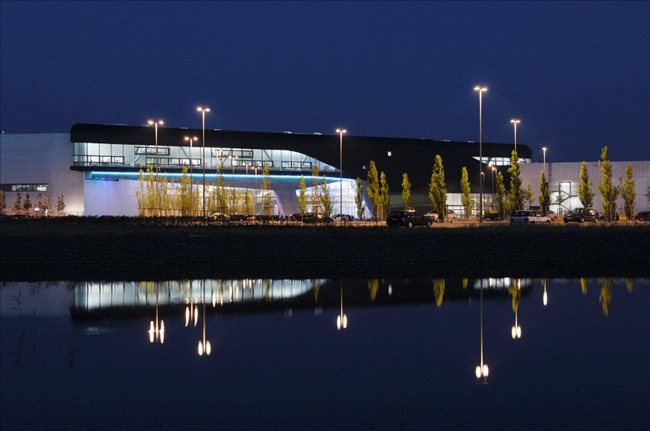
По сравнению с Лейпцигским заводом, завод BMW в Мюнхене выглядет старым и несовременным. Действительно,интересно то, что баварцы делают большую ставку на Лейпциг и имеют большие планы по расширению производства.
Наш гид объяснил нам, что завод имел четыре основных производственных зала (в BMW называют их "пальцы"). Им нужно было добавить новый зал ... и они добавили еще "большой палец"! (немецкий юмор). Но на самом деле, завод является очень гибким для выпуска новых продуктов.
Далее гид рассказал нам, что в Лейпциге будут производить новые i8 (Vision Concept) и i3 - городские электромобили, сделанные из карбона. Мы увидели некоторые образцы кузовов из углеродного волокна для нового i3/i8 (В 2014 году начнется производство в Лейпциге), а также узнали о планах на будущее расширение завода. Похоже, в BMW не только хотят, производить экономичный автомобиль (i3/i8), но они также планируют сделать завод – лидером в области энергосбережения, переработки и возобновления ресурсов.

Компания BMW планирует установить несколько ветровых электрогенераторов, которые будут обеспечивать нужды завода более чем на 90%. Также начнется строительство четырех новых крупных залов на территории завода. Интересный факт, о котором я не знал – территория завода BMW в Лейпциге в два раза больше исторического центра города.
Мы также видели некоторые образцы углеродных волокон (CF) для крыши новых M3/M6. Наш гид объяснил нам, что каждый килограмм, который сэкономили за счет преимущества в весе CF перед сталью, стоит в семь раз больше, поэтому использовать углеродного волокно приходится только там, где это действительно необходимо. Я, конечно, спросил его, почему в 1М не используется карбоновая крыша ... но он не знал!
Наша экскурсия началась в штамповочном и сварочном цехе. В этом зале стоял жуткий грохот. Было очень здорово видеть (в буквальном смысле) искры, и как панели кузовов, сваренные вместе, обретали очертания автомобиля.
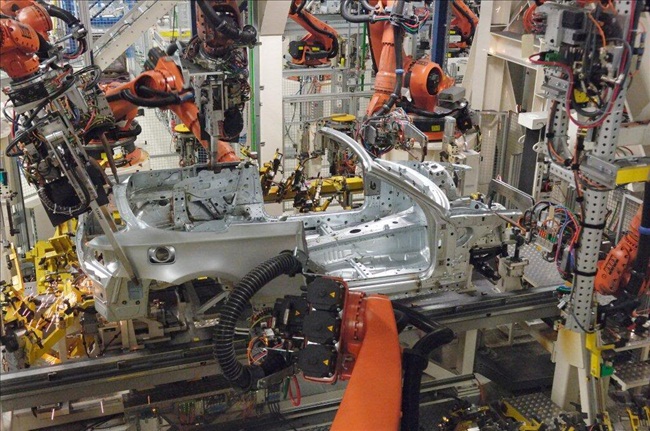
Восемьдесят пять процентов кузовных панелей изготавливаются на заводе. В BMW около 900 + роботов выполняют тяжелую работу - с помощью сварки, соединяют части вместе. В некоторых местах BMW использует эпоксидную смолу, но для большей части применяют старомодную сварку. Я заметил, что для E88 сварка днища поручена людям. Я предполагаю, что когда дело доходит до сложных элементов, люди справляются с этим гораздо лучше, чем роботы!
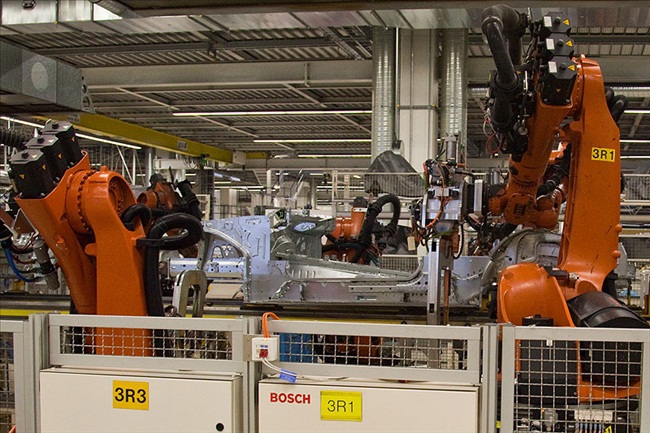
После того как кузова свариваются, они двигаются по конвейеру через лобби завода и все офисные помещения к окрасочному цеху, а затем на окончательную сборку. Это делается для того, чтобы все сотрудники ощущали свою причастность к общему делу.
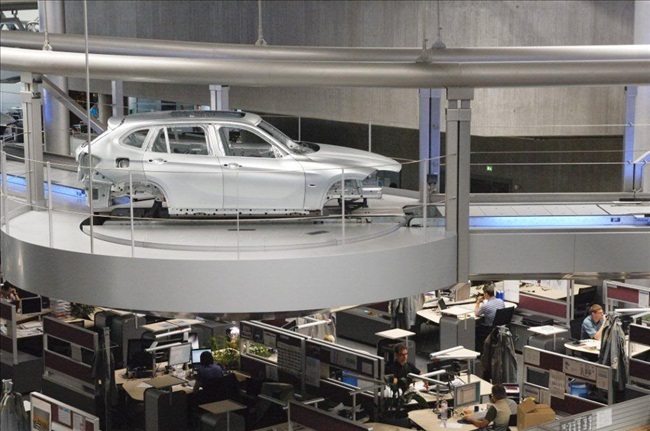
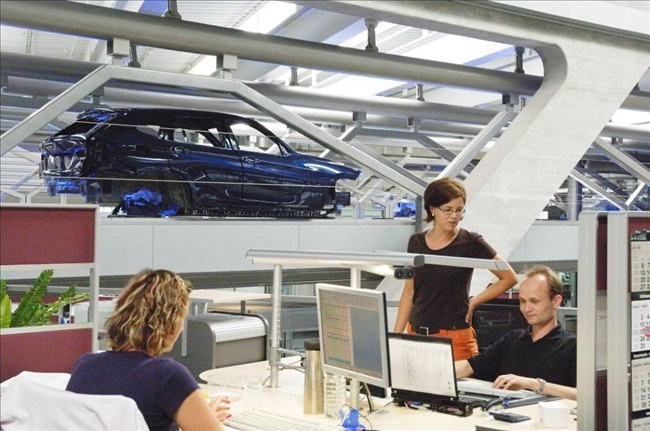
Затем мы посетили окрасочный цех. Обычно в подобных цехах очень грязно и на большинстве автозаводов посторонний человек не сможет попасть в окрасочный цех. Но в BMW конструировали этот завод с расчетом на проведение регулярных экскурсий и у них есть специальный герметичный коридор для туристов, которые могут полюбоваться на только что окрашенные автомобили. Технологии BMW позволяют окрасить один автомобиль в один цвет, а уже на следующий за ним автомобиль изменить цвет!
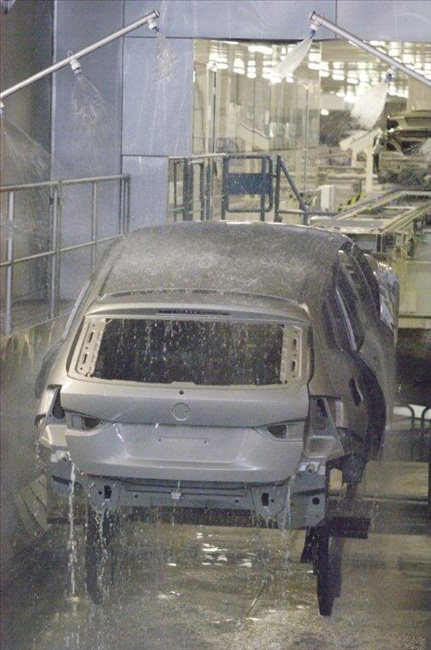
Здесь стоит отметить, что нам показали четыре этапа окраски: гальванизация, грунтовка, базовый слой, покраска (фактический цвет), нанесение прозрачного покрытия. На стене были представлены образцы "коллора", которые используются на производстве в Лейпциге.
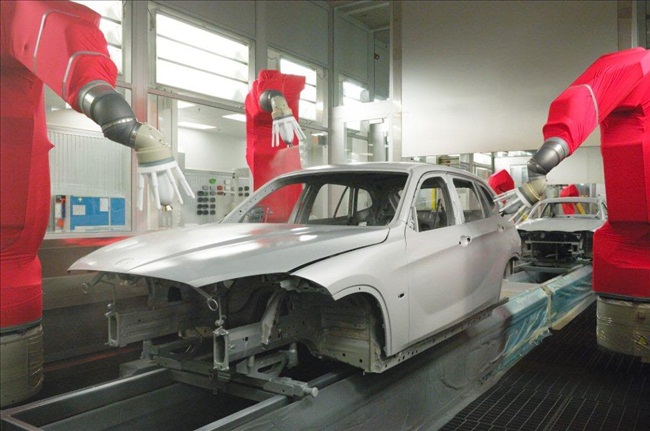
На один из них я обратил внимание - " Mineral White ". Я спросил нашего гида о том, что это за цвет, он ответил, что его используют на 1М! Но я усомнился: «вы имеете в виду Alpine White?». Он сказал, что он почти уверен, что в настоящее время используется Mineral White.
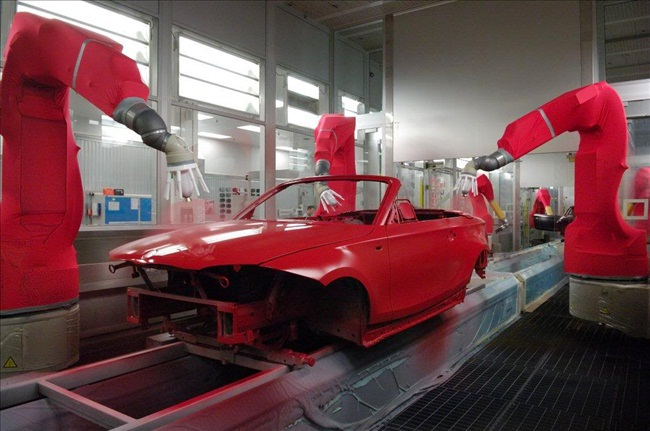
Я также видел " Uni-Schwartz ", который чем-то похож на DSB, но в нем больше черного.
Потом мы посетили пункт контроля качества окраски на конечной стадии. Здесь проверяют качество покраски каждой детали. Тут находилось всего несколько ребят, может быть, десять или около того. Я обратил внимание на две вещи – пол здесь был покрыт деревянным паркетом (что не типично для завода), а каждый работник может потратить столько времени, сколько он или она посчитает нужным, чтобы довести лакокрасочное покрытие автомобиля до идеального состояния.
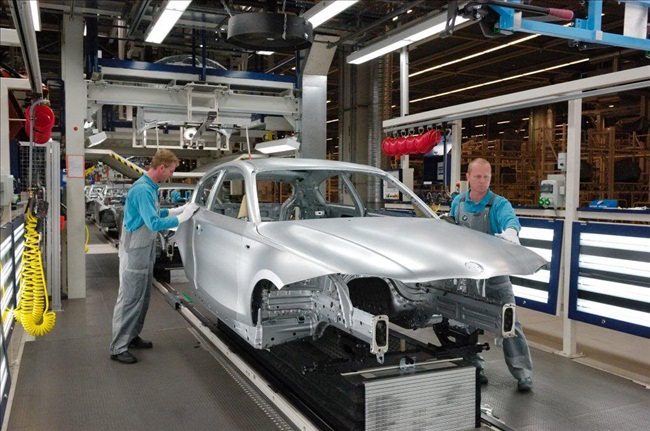
Работники используют маленькие двухдюймовые диски для мокрой пескоструйной обработки. Затем они тщательно полируют кузовные панели.
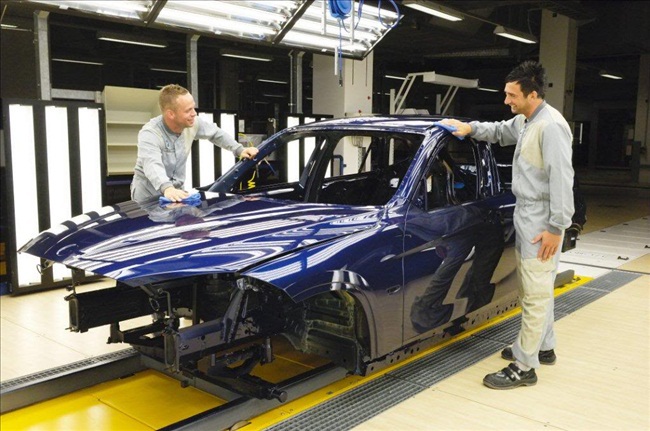
После того как сборка закончена ... какой-то процент готовых кузовов отправляется на склад. Это делается для того чтобы иногда при необходимости, изменить штамповочные прессы. И при этом на заводе всегда должен быть некоторый запас готовых кузовов, чтобы конвейер не останавливался. Я думаю, что примерно 900 автомобилей могут храниться внутри завода.
Затем мы прошли через сборочные цеха фабрики в зону "большого пальца", как наш проводник называл это место! Здесь кузова поднимаются на лифте на сборочный конвейер. Первое, на что обращаешь внимание - все двери снимаются и сохраняются для последующего использования. Теперь в машину укладываются жгуты проводов, звукоизоляция, приборная панель и устанавливаются стекла. Впечатляет то, как машину вращают, удерживая её на весу, за счет двух роликов.
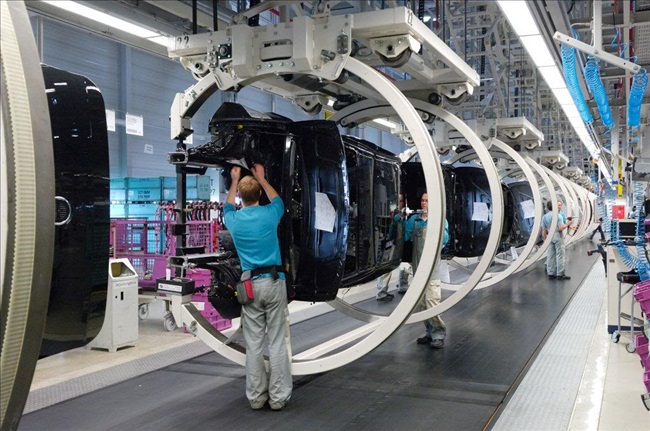
Мы поднялись на специальную смотровую площадку, которая расположена над заводскими цехами, вдоль всей "производственной линией" . Отсюда вы можете увидеть, как все рабочие трудятся на сборочном конвейере.
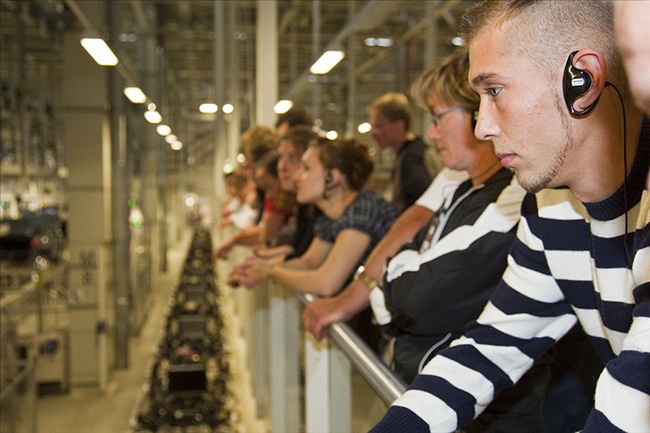
Любопытно, что никто здесь не делает одну и ту же работу целый день. Каждый сотрудник обучен выполнять несколько операций и они меняются каждые 45 минут - чтобы не скучать или не терять концентрацию.
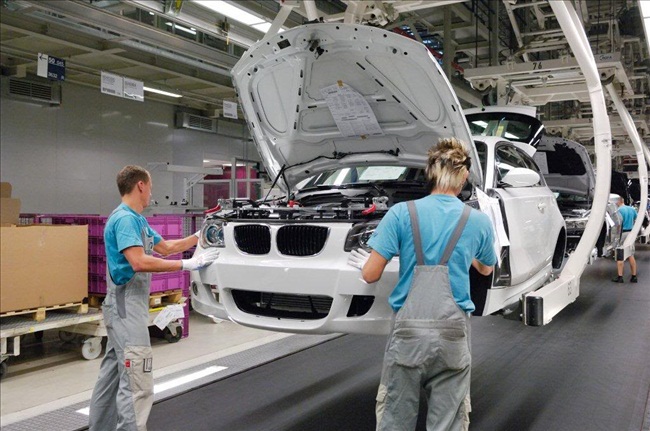
За все время нашей экскурсии мы видели около девяти 1M, собирающихся на заводе сегодня. Большинство из них были окрашены в фирменный цвет Valencia Orange. Но я был удивлен, увидев совсем немного белоснежных автомобилей (Alpine White). Я спросил нашего гида, BMW 1М каких цветов чаще всего заказывают? Он ответил, что большинство машин, которые он видел это Valencia Orange, затем по популярности идет цвет Alpine White, ну а самые редкие м-ки в черном цвете - Black Sapphire Metallic. Я думал, что цвета будут распределяться более равномерно.
По моему, все логично, белый цвет берут чаще, потому что это базовый цвет, за который не нужно доплачивать.
Мы также увидели немало ActiveE – электромобилей на базе купе первой серии E82. Для нас было неожиданностью, насколько сильно отличается передняя часть автомобиля от стандартной версии. Кроме того все ActiveE были окрашены в белый цвет, разумеется без ярких логотипов и полосок, которые мы видели на официальных фотографиях.
Продолжение и еще фотографии можно посмотреть в BMW блоге.